Rubber Capabilities, Rubber Engineering & Design Expertise
Shalimar is a R&D and Engineering focused company working to develop and deliver innovative solutions to our customers that allow them to achieve their goals. We support our customers with product design, material development, prototyping and production of precision molded rubber components.
Rubber Materials
Selection of the correct elastomeric rubber material for your application, be it fluid or environmental sealing, vibration isolation or dampening, impact bumpers, hoses and fluid movement and various other requires the review of numerous factors such as: dynamic or static application, system pressure, chemical compatibility; heat, cold and friction, material cost, design factors, installation practices, use of the product, product projected life and corresponding maintenance frequency.
Due to the number of interacting forces, it is STRONGLY RECOMMENDED THAT YOUR ELASTOMER SELECTION BE RIGOROUSLY TESTED IN THE ACTUAL APPLICATION, performance assumptions must be checked so that you are certain that all variables have been carefully considered.
Custom Compounds
Shalimar Rubber & Plastic, Inc houses a staff of knowledgeable chemist, elastomer design, and mechanical designers combined with an in-house rubber compounding laboratory to drive innovation for our customers. Our rubber compounding service can modify existing Elastomer's to produce custom polymers to meet application specific requirements or certifications. Working with organic, siloxane and carbon backbone Elastomer's, our custom rubber compounds can meet or exceed a wide range of product requirements. Our rubber compound batches are checked with strict control on quality assurance and tested using industry standard tests to produce physical, dynamic and rheological profiles. In addition, these profiles can be checked against customer provided requirements or application derived standards. This attention to detail helps assure consistency throughout the compounding process.
Prototyping
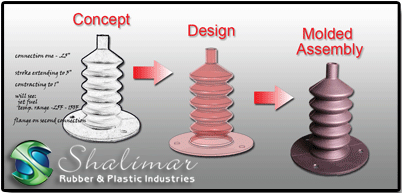
For concept to precision molded rubber components, Shalimar has an experienced dedicated team focused on helping our customers take their concepts from design to completed solutions through our rubber prototyping and design services.
Rubber product design expertise
Our team has extensive experience in designing components with rubber materials. Columbia engineers can assist our customers with:
Rubber product design expertise
Our team has extensive experience in designing components with rubber materials. Columbia engineers can assist our customers with:
Assemblies Manufacturing
Shalimar provides our customers with a range of component assemblies. These services range from component subassemblies to complete functional components with 100% in-line testing to customer specifications.
Our advanced ERP system supports flexible component sourcing options to allow for the integration of consigned, directed buy, and Columbia manufactured components into assemblies with corresponding lot tracking. Our team manages the supply chain to ensure that adequate component supply is maintained and that finished assemblies are delivered to our customers' manufacturing lines JIT.
Our advanced ERP system supports flexible component sourcing options to allow for the integration of consigned, directed buy, and Columbia manufactured components into assemblies with corresponding lot tracking. Our team manages the supply chain to ensure that adequate component supply is maintained and that finished assemblies are delivered to our customers' manufacturing lines JIT.
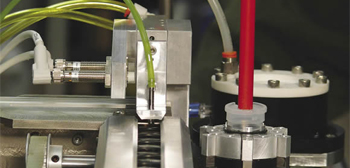
Injection molding

Shalimar utilizes the rubber injection molding processes to produce precision rubber molded components and rubber-to-metal bonded assemblies. The benefits of rubber injection molding are seen in high volume, tight tolerance, over-molding or precision applications.
Compression Molding
Shalimar utilizes the rubber compression molding process to produce a range of precision rubber molded components. The benefits of rubber compression molding are realized in a number of areas from low to medium volume applications and for some specialty high volume components.

Transfer Molding

Shalimar uses the rubber transfer molding process to produce a full range of precision molded rubber and rubber-to-metal bonded components. The benefits of transfer molding are seen in mid to high volume production, tight tolerance, over-molding and applications with colored or translucent materials.
Liquid injection molding (LIM)
Shalimar uses the liquid silicone injection molding process to produce a full range of precision near flashless molded silicone components and silicone over-molded assemblies. The benefits of liquid silicone injection molding (LIM / LSR) are realized in high volume, tight tolerance or over-molding applications.
