Rubber Injection Molding Process
Shalimar utilizes the rubber injection molding processes to produce precision rubber molded components and rubber-to-metal bonded assemblies. The benefits of rubber injection molding are seen in high volume, tight tolerance, over-molding or precision applications. The injection molding process can have a higher level of automation compared to other manufacturing processes such as compression molding or rubber transfer molding; with strict control over flash, waste, and quicker rubber cure times rubber injection molding is an optimal manufacturing method for many components.

Rubber Injection Molding Process Description:
The rubber injection molding process starts with an uncured rubber ribbon stock that is fed into a rotating screw of the injection unit. A controlled amount of material is pulled into the injection unit. Here the material is plasticized to a target elevated temperature. The rubber material is then injected into the mold cavity through a runner and gate system where it is held in the mold under high pressure and elevated temperature to activate the cure system in the rubber compound (rubber is vulcanized). The cycle time is established to reach an optimal level of cure. At the end of the cycle, the parts are removed or ejected from the cavities and the next cycle begins.Advantages of Rubber Injection Molding:
- Suits automation with automatic material feeding
- Complementary to high precision molding applications
- High level of repeatability
- Closed mold injection supports molding of complex geometries and overmolding
Disadvantages of Injection Molding vs. other rubber molding methods
- Higher start-up / shutdown costs, better suited for high volume applications
- Runner systems can lead gross material weights when cold runner systems or other low waste options are not utilized.
- Not all cure systems and elastomers are suitable for injection molding.
For more information on the rubber and plastic design processes please visit our rubber design section.
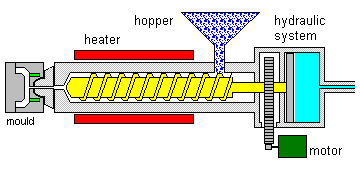
Rubber Injection Molding Steps:
- Material in injection unit ready for injection into cavity.
- Material is injected from injection unit through runner system & gates into cavities.
- Parts (material) are cured in mold until the cure process is completed.
- Molded rubber parts are removed from mold and the process is ready to begin again.